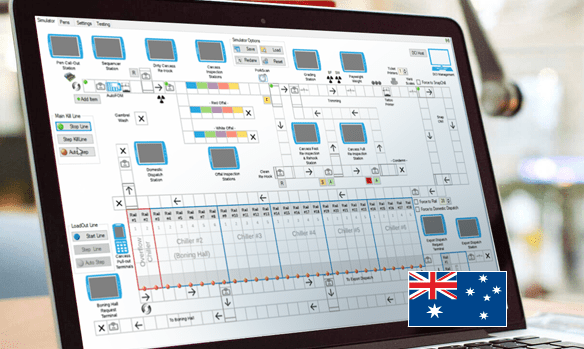
These projects range from fully integrated kill line systems where carcasses are managed from the beginning of the process through to the carcass chillers and dispatch to automated case weighing and labelling systems
Integrating factory floor has lead to innovations such as communicating customer requirements directly with cutting and trimming equipment on the kill line. This results in carcasses that meet individual customers specification leading to greater satisfaction. Other innovations include ‘hands-free’ case weighing, labelling and lidding, the labelling of products based on their chemical lean content and automated sorting of both case and carcass to the correct storage destination.
These projects have not only reduced the labour cost involved in these usually highly manual processes but have also lead to significant increases in throughput.
The Data Communications Interface (DCI.)
Integrating the equipment on the floor with the Emydex MES is a new module known as the ‘Data Communications Interface’ (DCI). This is the ‘intelligent hub’ that captures the data from the equipment and PLCs on the processing line and directs them as to how they are to act. Whether it is capturing the fat score from an in-line x-ray device and determining the final product code of the item, directing a robot to cut a carcass in a certain way or rejecting a carton for an illegible barcode, the DCI is the brains behind the process.
Using industry-standard communications protocols such as OPC or Telegrams, the system can be integrated into almost any existing production environment. Information collected from devices on the production line allows the Emydex MES to either manage a process or report on production in real-time. This allows production staff to react and manage the process during production rather than after the fact.
The Emydex Simulator
Production environments can be complex and high speed, production downtime is expensive and implementing new systems always carries risk. To reduce this risk and to allow modelling of the processes, Emydex has developed the Simulator module. This provides a graphical interface to the DCI and all the complex devices and control points in a production environment and can model the process from end to end. Each integration point in the process is replicated with the actual data that will be used in the live environment. This may be the output of a PLC or a piece of equipment used in production. This allows the end to end process to be tested without interrupting production thus providing full confidence in the systems ability to work in the live environment.
As part of the simulator integration, Emydex terminals can interact with the simulator and DCI allowing the terminals to run as they would in the live environment. This not only allows the human interface of the system to be tested but also proved a training environment for operators. With the simulator in place, operators can become fully conversant with the system before go-live.
The ability to test the ‘real’ environment in the back office ensures new systems are rolled out with the minimum of impact with staff fully trained and confident with the new environment.
Examples of the Simulator coupled with the DCI’s power include:
- Lariage pen management which direct staff to the next pen to empty reducing the time required to manually identify pens from paper-based systems.
- Kill line carcass processing robot control based on customer requirements or processing issues.
- The use user defines carcass rules that allow carcasses to be managed before grading for increased kill line efficiency.
- RFID gambrel tracking ensures carcasses are processed accurately and efficiently. Carcases can be directed automatically to retain/detail rails based on carcase faults, traceability is guaranteed and by automating sorting into the chillers, boning rooms can run more efficiently.
- Chiller sortation rules that maximise chiller efficiency and automate the put-away process.
- Carcase cutting and put away based on rules generated from the kill data reducing the labour required for cutting and storage. With information being passed to carcasses quartering or portioning system and the resulting portions being directed to the correct locations for boning or dispatch, manual sorting and pushing of carcasses can be removed.
- The determination of the correct product code for an item based on its actual fat score reducing CL issues and customer claims.
- Automated weighing and labelling of cartons and crates reducing labour and ensuring the consistency of barcode placement for subsequent scanning.
- Automated carton sorting to reduce labour in manual carton handling.
Emydex Business Intelligence Reporting (BI)
Information is only useful if it is timely, relevant and easy to understand. This is where the new Emydex BI Reporting tool excels. This module allows end-users to extract data not only from the Emydex system but also from third party system and presents the information in a way that is meaningful, timely and clear. Reports can be run from a Web browser or back-office client allowing information to be available for all authorised staff anywhere in the world at any time.
Given the BI tool can report on any information in the Emydex MES and the DCI directly, it can display production information such as throughput speeds, real-time giveaway, production yields, grading scores, contaminant rates etc. and highlight to the Production team if an issue arises.
Information is also available from the sales, kill line payments, inventory, quality management and purchasing module, in fact, any area of the Emydex system. This allows users to generate their own sales analysis, livestock performance, inventory holding reports etc. and to display information in a way that is meaningful to them.
Reports can be automatically generated and published on a schedule allowing management to receive a summarised report of the day's activities based on key performance indicators with alerts to allow for the identification and correction of issues before the next day.
Summary.
With the integration of the production floor into the Emydex MES and the ability to control and report on production processes in high-speed environments, the Emydex MES has reached a class-leading status. Combined with the Emydex BI Reporting tool, production processes and any associated activities can be reported upon and managed real-time reducing reworks and loss.
For example, by reporting on contamination on a kill line or increased give-away on a high speed labelling line, changes can be made in the production environment to correct these to lessen the impact on the current production. This, combined with the reduction in labour and increased efficiencies in conjunction with the well-established ease of use and flexibility of the Emydex system mean existing Emydex user can gain immediate advantage from the introduction of these modules.
New customer will find the Emydex MES an extremely powerful solution for the management of their food processing environment.
Share the results easily with the ability to export the entire dashboard results, or an individual widget at the press of a button.
Individual dashboards can be set up with automatic refresh rates, meaning your data is always up to date!
If you want to learn more – contact Ireland, Australia, South Africa or North America offices