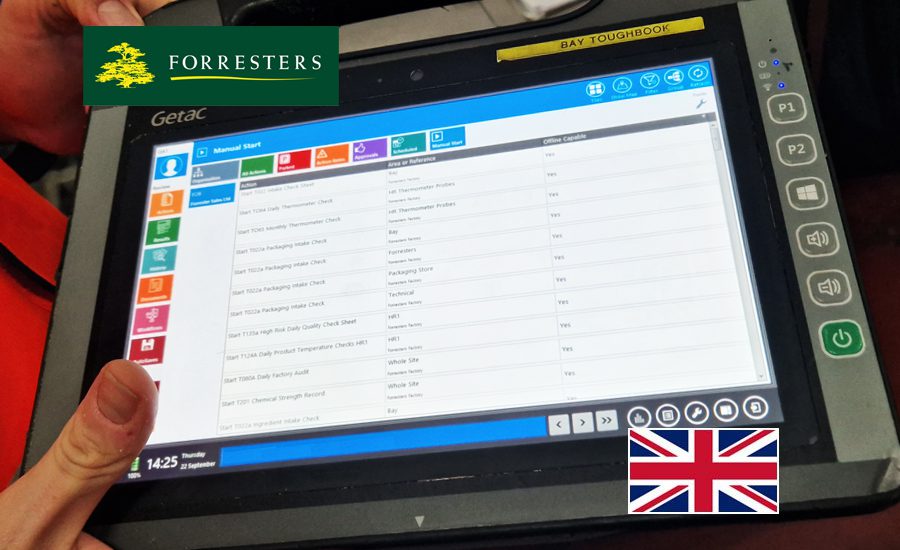
Over the past ten years, Forresters Chicken has leveraged Emydex's Quality Management system to enhance accuracy, reduce human error, gain real-time insights into quality data, and improve traceability. This collaboration has significantly transformed Forresters Chicken's operations, ensuring the highest standards of quality and efficiency in their processes.
Meet the Client
Established in 1972, Forresters is one of the largest suppliers of cooked, raw, and coated poultry in the United Kingdom. Based in Cheshire, the company provides retailers, food services, pub retailers, manufacturers, and catering butchers with frozen, chilled branded, and own-label chicken products. To maintain its reputation for high-quality standards, Forresters set out to enhance its quality management processes.
The Opportunity
With a growing client base and increasing production demands, Forresters required a more streamlined and robust approach to quality management. Existing manual quality checks were resource-intensive and prone to human error, especially as production volumes rose. Furthermore, limited real-time access to quality data hindered swift decision-making and posed challenges in meeting regulatory standards.
Forresters needed a comprehensive Quality Management System (QMS) that could automate quality workflows, provide real-time data, and integrate with their ERP system for seamless traceability and compliance tracking. Forresters had been operating an Emydex factory floor MES (Manufacturing Execution System) for production control, yield management and traceability reporting for many years, so it was a straightforward decision to extend our Emydex software footprint to include all of our Quality, Compliance and Food Safety Management processes.
What We Did
Working closely with Forrester’s management, our team worked with Emydex to develop and implement a customised QMS solution that aligned with Forrester's operational goals. The implementation process was structured in two main phases:
1. Phase One - Digitalising Quality Checks
Forresters began by introducing automated digital checklists across the production floor, replacing paper logs and allowing quality checks to be completed via tablets at each workstation. Data is now collected on tablets running the Emydex Quality system in real-time, and any deviations from standards trigger instant alerts, allowing issues to be addressed immediately.
2. Phase Two - Comprehensive Quality Dashboard
In the next phase, Forresters deployed an Emydex quality system dashboard for management and supervisors, providing a centralised view of quality metrics across production. The dashboard consolidates data on batch compliance, audit trails, incident reporting, and corrective actions. Fully integrated with Forrester's ERP system, it links directly to purchasing and inventory data, ensuring traceability from raw materials to finished products.
3. Automated Audit and Compliance Reporting
A key feature of the Emydex EQMS is its automated compliance reporting. The system generates real-time, auditable compliance reports accessible from any device, dramatically reducing the time required for internal and external audits. Issues are flagged and assigned for resolution, enhancing accountability across departments.
The Results
Since implementing the Emydex Quality Management system, Forresters has significantly improved operational efficiency and quality compliance.
Enhanced Accuracy and Reduced Human Error: Automated digital checklists have replaced manual entries, reduced errors and ensured consistency in quality checks across all lines.
Real-Time Quality Insights: Managers and supervisors can now view quality metrics instantly, enabling quick decision-making and proactive quality control.
Efficient Compliance Audits: Compliance reporting, which previously required days of preparation, is now generated instantly by Emydex, saving time and resources. Audit readiness has also improved, as records are automatically archived and easily accessible.
Improved Traceability: The QMS enables complete traceability from raw material intake to finished product distribution, facilitating stock rotation and maintaining quality at every stage.
Feedback from Key Stakeholders
Dwayne Chin, Head of Technical at Forresters, noted, “The Emydex QMS has been transformative for our business. Our team no longer spends hours sorting through paper logs; we can spot and address issues immediately. Compliance reporting that once took days is now ready in minutes, giving us more control over quality and peace of mind.”
John Acornley, Finance Director, added, “With the Emydex Quality system in place, Forresters have significantly reduced errors and improved our response times. The Emydex automated alerts keep our team informed, and the dashboard makes it easy to stay on top of production quality. It’s been a huge upgrade.”
Summary
The Emydex Quality Management System implemented at Forresters has streamlined operations and reinforced its commitment to delivering high-quality products to its clients. By enhancing workflows, improving traceability, and enabling instant access to quality data, the QMS has empowered Forresters to meet regulatory standards and confidently scale its operations.
Don't wait! Embrace the future of quality management with Emydex's Electronic Quality Management Software (EQMS).
If you want to learn more – contact Emydex in any of our global market offices in Ireland, Australia, New Zealand, South Africa, or North America