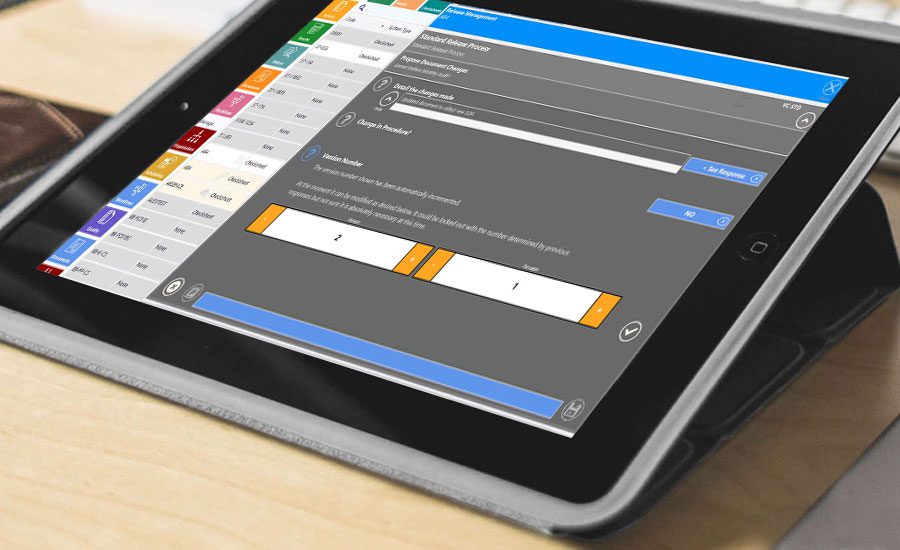
Meat, Fish, and Food Processors Rejoice!
Ditch the Paperwork with Emydex Quality Management
Gone are the days of mountains of paper checklists and spreadsheets! For meat, fish, and food processors seeking a streamlined, efficient, and data-driven approach to quality management, a revolutionary solution has arrived: Emydex’s electronic quality management software (EQMS) system.
This innovative software eliminates the hassle of manual record-keeping, transforming the way you handle quality surveys and workflows.
Here’s how it elevates your operations:
- Effortless Data Collection: Say goodbye to handwritten forms & excel. Capture quality data electronically on mobile devices, tablets, or computers, saving time and reducing errors.
- Real-time visibility & notifications: Gain immediate access to quality data across your entire operation. Identify trends, pinpoint potential issues, and make informed decisions faster. Get notified when issues occur in production.
- Enhanced Compliance: Ensure adherence to food safety regulations and industry standards with pre-built templates and automated workflows. Reduced Paperwork: Reduce paperwork by up to 90%, save storage space, and go green with a paperless system.
- Improved Collaboration: Share quality data seamlessly between teams, fostering better communication and transparency.
- Data-Driven Insights: Generate comprehensive reports and analyse trends to identify areas for improvement and optimize your quality control processes.
Realise the benefits:
- Reduced Costs: Save time and money spent on managing paper-based systems.
- Improved Productivity: Streamline workflows and free up valuable employee time.
- Enhanced Food Safety: Proactively identify and address potential risks, ensuring
the highest quality products. - Increased Customer Confidence: Demonstrate your commitment to quality with a
robust and transparent system.
Meet the customer:
Dawn Meats is a family-owned business established in Co. Waterford, Ireland in 1980, and has grown to become one of the largest and most important beef and sheep processing groups in the industry. The group employs over 8,000 people in dozens of countries, including 10 sites in Ireland and 13 in the UK, exporting to over 50 countries worldwide.
Every year, Dawn Meats processes over 1 million cattle and 3.5 million sheep, generating more than €2.5 billion in turnover for the company and contributing over €1.67 billion to rural
economies through 30,000 farms in Ireland and the UK. The numbers are staggering, and so is their success.
When Dawn Meats wanted to streamline its quality management system operating on its factory floors, it turned to Emydex. Five years later, Dawn Meats in Ireland and its UK division, Dunbia, operate Emydex’s EQMS system in 15 manufacturing plants, across 13 sites.
What’s Unique?
What is unique about the Emdyex EQMS system is its ability to operate across multiple plants, divisions, and geographies. The Emdyex EQMS system is ideally suited for larger, group-type meat, fish and food processors, those like Dawn Meats operating multiple plants, potentially across multiple countries.
For example, the group technical manager for Dawn Meats has a real-time view of quality across the entire organisation from their laptop. The Technical Manager for Ireland has a view of their plants operating Emydex EQMS in Ireland, and the same for their UK technical manager. Equally, each plant technical manager has a view of their plant QC data. Even though the system has been designed with multi-plant processors front of mind, this Quality system is suitable for single-plant/stand-alone food processors also.
In their words!
“Seeking a solution for collecting quality data in an effective, sustainable manner and utilising this data efficiently, Dawn Meats Group partnered with Emydex to deliver an electronic quality management system for the betterment of food safety & quality in our factories.
We selected Emydex, a long-standing partner of ours, due to Emydex’s understanding of our food production facilities, their excellent software development ability and personal project management delivery.
The Electronic Quality Management System is an innovative, adaptable software solution which fulfils our needs and continues to evolve through more areas of our factories, making them fit for the future. I would like to congratulate Emydex on the success of this project and look forward to our continued partnership in the future.”
Julia Hewerdine, Group Food Safety & Quality Project Manager with Dunbia & Dawn Meats Group
“The result is that resources have been freed up, saving cost. Less paperwork, collection is instant, no errors, less time, no printing, archive space has been freed up, we have instant and easy retrieval of documents – everything has improved and is more accurate.
We got what we wanted which is improved collection, visibility and use of our data. That instant visibility means we have real-time situation reports. The tangible savings are obvious- less paper and less ink, for example. The less obvious savings are evident too – less time and effort, fewer mistakes and corrections, reduced hold-ups, etc. I can see if people are making the required quality checks and if they are making them at exactly the right times.
Working with Emydex has been great – they understand their system and have been very helpful. Emydex created a system for support that includes excellent on-going communication. We have worked with them over the past decade on traceability, and so we trusted them. I like how their QMS system is so flexible, and how they could configure it to how we wanted to work – not something you get with an out-of-the-box solution. That flexibility meant that we were given artistic license as to how to develop our own workflows.”
John Coleman, Dawn Group Technical Manager in Ireland
“The Emydex Quality Management System offers Dawn Meats plants the ability to instantly deliver quality data during customer audits, easing what once before would have been a page-flicking exercise. Auditors have had a positive outlook on the system, frequently commenting on its benefits of generating reports, assigning close-outs, and collating data at the click of a button.
The paperless system has improved its usability, as users often remark how much quicker it is to find specific paperwork. The system’s simplistic layout has also been beneficial for training, as the checks are easily found under Scheduled and Manual Start Action.
The Emydex Electronic Quality Management System has had a tremendous impact on our data collection on site, as well as safeguarding the completion of checks in a scheduled and timely manner. Its reliability and speed have ensured that workflows carried out have been given full attention, and no corners are cut.
The system, post workflow completion, offers users the opportunity to view data instantly, and if any issues occur, they can be investigated immediately. The Client extends a library of data to be trended, which in an audit, is a useful tool to safeguard compliance with customer standards.
Easing away from paper-based checks, the system has allowed users to access checks timelier, with the ability for the data to be instantly trended for various stakeholders. Users, especially QA’s, are fond of the ability to save various checks within the factory, without needing to return the checks to allocated folders, which would previously have occurred. Thus, the systems speed and performance has allowed for advancements in thorough checks on the line, as well as increasing their time to carry out additional daily checks, without needing to carry out tedious admin tasks.”
Alan McCormack, Technical at Dawn Meats Group
Don’t wait! Embrace the future of quality management with electronic quality management software.
If you want to learn more – contact Emydex in any of our global market offices in Ireland, Australia, New Zealand, South Africa, or North America