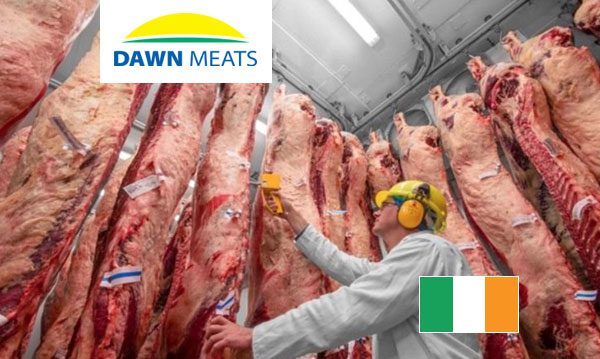
Dawn Meats is an outstandingly successful meat processing group. When they wanted to streamline their quality management system on the factory floors, they turned to Emydex
Meet the client
Dawn Meats is a family owned business that was established in Waterford, Ireland in 1980 and has grown to become one of the largest and most important beef and sheep processing groups in the industry. The group employs over 7,000 people in dozens of countries, including 10 sites in Ireland and 12 in the UK, exporting to over 50 countries worldwide.
Every year, Dawn Meats processes over 1 million cattle and 3 million sheep, generating more than €2 billion in turnover for the company and contributing over €1.67 billion to rural economies through 30,000 farms in Ireland and the UK.
The numbers are staggering and so is their success.
The opportunity
Dawn Meats developed their own in-house quality management system which largely relied upon manual, paper-based checks all along their factory floors.
While this was rigorous and helped to maintain the very highest levels of quality products for the company, it was inefficient, creating delays, tons of paper, hours of data entry and leaving the door open for error. The old manual way of working involved lengthy printing, handing out, filling in, returning, checking, countersigning and storage of paper records. On top of that, files had to be physically retrieved in the event of audit.
“Dawn Meats wanted to do away with paper-based quality checks along the floor and to use the data they collect in a far more efficient manner to drive improvements. They wanted a quality management system that would create actions and alerts automatically, so that managers could see in real time what has been done. This would mean they could make more informed decisions and corrective actions, improve compliance and reduce issues.”
David McMahon, Emydex CEO
Since 2013, Emydex have being developing their Quality Management System capable of being used in single site as well as across multi-site Group processors like Dawn Meats. Emydex’s Enterprise Quality Management System (EQMS) is, in short, a software system that allows food processors carry out their factory and supplier quality and audit checks on tablets, reporting instantly in the back-office, replacing all paper-based quality check sheets on the factory floor.
A perfect fit for Dawn Meats.
What we did
There were five main drivers behind Dawn Meats decision to select Emydex
The first was Emydex gave them a single system, with our quality module sitting alongside all other Emydex factory floor Production or Warehousing modules on a common platform.
Next, our solution can be fully integrated to shop floor industrial machinery, capable of scanning barcodes, meaning no manual keying of data needed.
Thirdly, the Emydex EQMS system can be installed on-premise or in the cloud. Emydex don’t force customers to operate their QMS out of the cloud, they can install on-prem if required.
Another key differentiator is the system can work off-line as well as on-line for all compatible mobile devices, using local databases. Meaning operators can switch to off-line mode when capturing quality data in areas with poor or zero wi-fi coverage.
Finally, the system is very configurable in-house including an easy to use QC workflow builder tool. This function allows in-house QC personnel (non-IT people) to design and build their own Quality workflows in-house, including QC surveys, QC check-sheets and quality audits, without the need to involve either Emydex developers or their internal IT department.
Going Live
The Emydex EQMS system has been running in at Dawn Meats Irish facilities in both Rathdowney and Carroll’s Cross plants for a number of months.
At this point Dawn’s group technical QC team have configured internally almost 200 separate QC workflows in Emydex including for example, Abattoir and Boning hall pre-op checks, GMP audits, metal detector checks, glass and hard plastic, knife register and attendance checks etc.
Once built centrally, such workflows can then be used across all the group’s sites. Having completed site testing over the past number of weeks, the system is currently being rolled out to Dawn’s remaining processing plants in Ireland including Grannagh, Ballyhaunis, Charleville and Kilbeggan.
The results
Emydex EQMS helps Dawn Meats to streamline the QMS processes across their factories and to ensure they are working to the most effective QMS system. As it standardises the QMS and FSM systems across the group it improves compliance and shares best practice throughout all of the facilities.
Using the Document Management System included within the system, sites can share generic documents and processes, and tailor the specifics to the site. This reduces time lost in writing up documents and figuring out procedures and risk assessments.
The system creates actions, alerts, notifications and alarms in real time and automatically tells them when they are out of compliance, forcing the immediate implementation of corrective actions.
It improves compliance and reduces issues in announced and unannounced audits, reducing risk with defective product, product recalls and customer satisfaction.
The Emydex system frees up resources to drive product quality improvements and also frees up archive space and storage. It will give central management a holistic view through instant visibility of all factories in one centralised system, making KPI reporting easier and that maximises safety, quality and compliance.
Finally, this accurate QMS data can drive operational processes and business decisions, helping continuous improvement by providing instant effect data.
In other's words
Speaking shortly after the Emydex system go-live in Dawn’s second site at Carroll’s Cross, John Coleman, Dawn Group Technical Manager in Ireland said,
“The result is that resources have been freed up, saving cost. Less paperwork, collection is instant, no errors, less time, no printing, archive space has been freed up, we have instant and easy retrieval of documents – everything has improved and is more accurate.
We got what we wanted which is improved collection, visibility and use of our data. That instant visibility means we have real-time situation reports. The tangible savings are obvious – less paper and less ink, for example. The less obvious savings are evident too – less time and effort, fewer mistakes and corrections, reduced hold-ups, etc. I can see if people are making the required quality checks and if they are making them at exactly the right times.”
Working with Emydex has been great - they understand their system and have been very helpful. Emydex created a system for support that includes excellent on-going communication. We have worked with them over the past decade on traceability, and so we trusted them. I like how their QMS system is so flexible, and how they could configure it to how we wanted to work – not something you get with an out-of-the-box solution. That flexibility meant that we were given artistic license as to how to develop our own workflows.
John Coleman
Dawn Group Food Safety and Quality Manager
What’s next?
The next phase is roll out Emydex’s EQMS to all 8 Dawn Meats factories in Ireland. Over 2020 the system will be introduced to Dawn’s sites in the UK.
For more on Emydex's Quality Management system, read:
Electronic Quality Management Systems for the Food Industry
or contact Sales in any of our Dublin, Brisbane, South Africa or Toronto offices