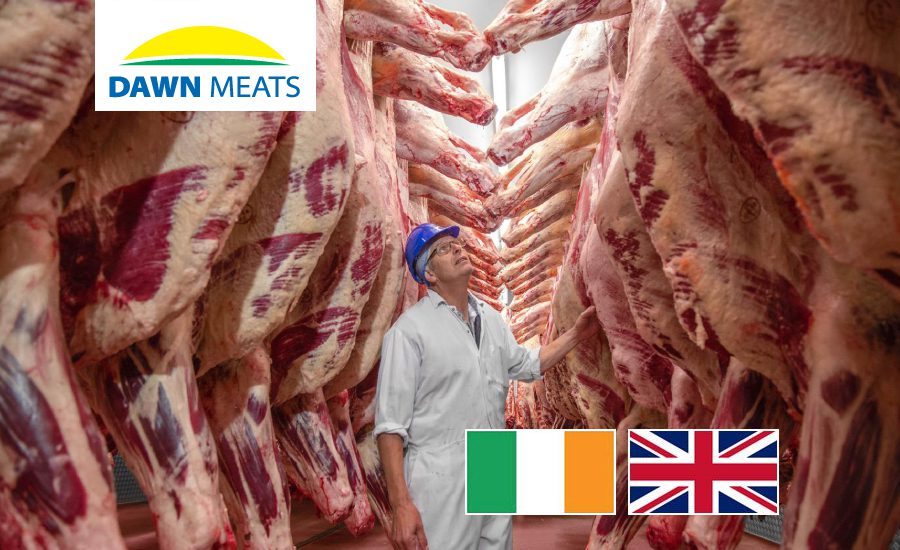
Dawn Meats Group, one of Europe’s leading meat processing companies, sought to streamline its factory-floor Quality Management System with Emydex.
Meet the client
Dawn Meats Group is a family-owned business established in 1980 in Waterford, Ireland. The company has grown to become one of the largest and most important beef and sheep processing groups in the industry. The group employs over 8,000 people across twelve countries, including ten sites in Ireland and thirteen in the UK, and exports to over 50 countries worldwide.
Every year, Dawn Meats Group processes over 1 million cattle and 3.5 million sheep, generating more than €2.5 billion in turnover for the company and contributing over €1.67 billion to rural economies through 30,000 farms in Ireland and the UK.
The numbers are staggering, and so is their success.
The Opportunity
Dawn Meats developed its own in-house quality management system, which largely relied on manual, paper-based checks throughout its factory floors.
While this was rigorous and helped to maintain the company’s highest quality products, it was inefficient, creating delays, tons of paper, and hours of data entry. The old manual way of working involved lengthy printing, handing out, filling in, returning, checking, countersigning, and storing paper records. On top of that, files had to be physically retrieved in the event of an audit or to trend data.
For the past decade (since 2013), Emydex has been developing an Electronic Quality Management System (EQMS) capable of being used in single plants as well as across multi-plant group processors like Dawn Meats Group
Emydex’s Quality Management System is a software system that allows food processors carry out their factory and food safety quality and audit checks on tablets, reporting instantly in the back-office, replacing all paper-based quality check sheets on the factory floor.
A perfect fit for Dawn Meats Group.
“We selected Emydex, a long-standing partner of ours, due to Emydex’s understanding of our food production facilities, their excellent software development ability and personal project management delivery,” said Julia Hewerdine, Group Food Safety & Quality Project Manager in Dawn Meats Group.
There were several drivers behind Dawn Meats Group’s decision to select Emydex:
One System
The first was Emydex gave Dawn Meats Group one single system, with Emydex’s quality module sitting alongside all other Emydex factory floor MES, Production and Warehouse Management modules on one common platform.
“We have worked with Emydex over the past decade on the production and traceability side, so we trust them”, commented John Coleman, Dawn Group Food Safety and Quality Manager.
Cloud or On-Premises
The EQMS system can be installed on-premises or in the cloud. Emydex doesn’t force its customers to operate their QMS out of the cloud; they can install it on-prem if necessary.
“Emydex has had a tremendous impact on our shop floor quality data collection on site, as well as safeguarding completion of checks in a scheduled and timely manner. Its reliability and speed have ensured that workflows carried out have been given full attention, and no corners are cut.” said Alan McCormack, Dawn Meats Technical Team
Online and Offline Mode
Another key differentiator is that the system can work offline as well as online for all compatible mobile devices, using local databases. This means operators can switch to offline mode when capturing quality data in areas with poor or zero Wi-Fi coverage.
“Our QA’s like the systems’ ability to save checks within the factory, without needing to return the checks to folders which would previously have occurred. The system’s speed and performance has allowed for more thorough and detailed checks on the line, as well as increasing their time available to carry out additional checks, without needing to carry out tedious admin tasks.”, commented Alan McCormack, Dawn Meats Technical Team.
Flexibility
Finally, the system is very configurable in-house including an easy-to-use quality workflow builder tool. This function allows in-house QC personnel (non-IT people) to design and build their own Quality workflows in-house, including QC surveys, QC check-sheets and quality audits.
“I like how their QMS system is flexible, and how we can configure it to how we wanted to work – not something you get with an out-of-the-box solution. This flexibility means we can build our own workflows ourselves, not involving Emydex nor internal IT.” added John Coleman, Dawn Meats Group, Food Safety and Quality Manager.
Going Live
The Emydex Quality Management System has been operating in Dawn Meats Group’s Irish & UK facilities for over five years now. Having first gone live in two Irish plants in 2019, today the system is operating in Dawn Meat’s seven primal processing plants in Ireland, as well as a further seven group primal processing plants in the UK, fourteen plants so far, with further roll-outs underway, including three retail processing plants in the UK.
At this point Dawn’s group technical QC team have configured internally almost 500 separate QC workflows in Emydex including for example, Abattoir and Boning Hall pre-op checks, GMP audits, metal detector checks, glass and hard plastic, knife register, and attendance checks etc. Once built centrally, such workflows can then be used across all the group’s sites.
The Results
Emydex EQMS helps Dawn Meats Group streamline the QMS processes across its factories and ensure they are working to the most effective QMS system. Standardising the QMS and FSM systems across the group improves compliance and shares best practices throughout all the facilities.
“External auditors have had a positive outlook on the Emydex quality system, frequently commenting on its benefits of generating reports, assigning close-outs, and collating data at a click of a button.” said Alan McCormack, Dawn Meats Technical Team
Using the Document Management System included within the system, sites can share generic documents and processes and tailor the specifics to the site. This reduces time lost in writing up documents and figuring out procedures and risk assessments.
The system creates actions, alerts, notifications and alarms in real-time and automatically tells them when they are out of compliance, forcing the immediate implementation of corrective actions.
“The less obvious savings are evident too – less time and effort, fewer mistakes and corrections, reduced hold-ups, etc. I can see if people are making the required quality checks and if they are making them at exactly the right times.” John Coleman, Dawn Group Technical Manager in Ireland
It improves compliance and reduces issues in announced and unannounced audits, reducing risk with defective product, product recalls and customer satisfaction.
The Emydex system frees up resources to drive product quality improvements and frees up archive space and storage. It will give central management a holistic view through instant visibility of all factories in one centralised system, making KPI reporting easier and maximising safety, quality and compliance.
“The result is that resources have been freed up. Less paperwork, collection is instant, no errors, less time, no printing, archive space has been freed up, we have instant and easy retrieval of documents – everything has improved and is more accurate.” commented John Coleman, Dawn Group Technical Manager in Ireland
Finally, this accurate QMS data can drive operational processes and business decisions, helping continuous improvement by providing instant effect data.
“The Emydex Quality System is an innovative, adaptable software solution which fulfils the needs of Dawn Meats Group and continues to evolve through more areas of our factories, making them fit for the future.”
Julia Hewerdine, Group Food Safety & Quality Project Manager in Dawn Meats Group
Don’t wait! Embrace the future of quality management with electronic quality management
software.
If you want to learn more – contact Emydex in any of our global market offices in Ireland, Australia, New Zealand, South Africa, or North America