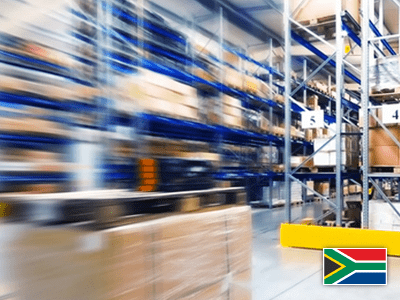
Following on from previous successful implementations in Southern Africa, together with Summit Process Solutions, Emydex has rolled out three additional cold store projects for three new customers in South Africa. These include the Emydex Cold Store Warehouse Management System to QK Cold Store South Africa, located in Johannesburg, as well as to Table Bay Cold Storage and GPS Food Group RSA, both located in Cape Town. Over the past 18 months, the Emydex development team have added new functionality to the Cold Store module such as a Web Client, Stock Maps and EDI Integration.
QK Cold Stores
QK Cold Store SA offers a wide range of solutions from case picking to blast freezing, tempering, re-palletising and container loading on the deck, as well as offering a primary transport solution.
QK Cold Store SA had a requirement for a Full Warehouse Management System, capable of covering their four operational warehouses.
In phase one, Emydex implemented its Warehouse and Production Management modules, providing QK SA with a full solution from intake right through to dispatch. The project went live in October 2017, streamlining its operational processes. They now have functionality for operators to use handheld scanners to catch all movements of stock in real-time, allowing them to track all stock in their Cold Stores.
Further phases are scheduled for 2019 and will include integrating with customers’ systems, through EDI functionality, giving customers more visibility over stock sent to QK, stock being held in the Cold Store and stock that has been dispatched, in real-time.
GPS Food Group RSA
GPS Food Group provides sales, marketing, and stock control services from the UK for the sale of BMC, MeatCo and additional customer products in Europe.
GPS Food Group UK, an existing Emydex client, acquired a facility in Cape Town, with plans to build a Cold Store and later extend to a Value-Added Processing Plant. GPS approached Emydex in 2017 to advise of the project requirements which were to be broken into two phases.
Phase one of the project kicked off with Cold Store functionality including stock intake, SDA Warehouse functionality, Dispatch and Client Invoicing. Later in the year phase two began, implementing the Emydex Production and Traceability reporting modules which covers their Value-Added processing operations in the same plant. This included adding functionality to cover 3rd party raw materials intake, de-boxing, de-frosting, processing, ingredients dispensing, recipe formulation, tumbling & injecting, cooking, packing, order picking and dispatch, all with full product traceability and yield monitoring.
Web Client – Distribution Warehouse System
Emydex, in conjunction with cold store customers in Southern Africa, developed a web interface that links directly to the Emydex customer database.
As a part of the DWS application, customers will be able to create Advance Shipping Notes (ASN) remotely. These ASN’s are then able to be allocated to a purchase order and will help to eliminate human error and increase the efficiency of the intake process at the Cold Store.
Additionally, their customers will also be able to create dispatch orders remotely, enabling them to create work orders, directing the cold stores to dispatch products. These work orders specify which product, how many, when and what destination the product is to go to.
As well as this, their customers can drill down into their stock that is on-site, enabling them to look at quantity of product(s) they have, batch numbers and other relevant traceability information. Emydex will also be implementing functionality to allow their customers to put product onto Quality Control hold, meaning that when a recall occurs product can be put on hold instantly and remotely as required.
Stock Maps
Some of the Cold Store systems delivered also include the latest version of Emydex’s Stock Maps functionality, enabling Cold Stores to view and search against a visual representation of their stocks, by drilling down through areas and warehouse locations, and interrogating stock via graphical views of racks, rows and bays. This latest version of Emydex Stock Maps system enables Emydex customers to configure, build and maintain Stock Map views themselves in-house via an easy-to-use Stock Map configuration editor. This allows the virtual representation of the cold store to be able to mimic the physical layout of the customers actual warehouse.
EDI Integration
Customer files containing high levels of detail of stock sent to the cold stores, are imported into Emydex, in order to let managers, see purchase orders, inventory levels and product details such as quantity and weight coming into the Cold Stores. Operators can validate that they’ve received the correct stock using handheld scanners, which feeds the information back into Emydex, speeding up the process of data exchange and eliminating the need for paperwork or phone calls.
Summit Process Solutions Hardware & Aftersales Support
Together with SPS’ industrial waterproof hardware such as the reliable PT9000 – 17” Touch Screen Waterproof Shop Floor Computer and Industrial Stainless-Steel Smart Scales, integration is seamless and simplifies while speeding up operations to our customers’ maximum benefit. SPS have been a loyal partner when it comes to supplying either – hardware, training of customers, aftersales service or supplying of relevant information, to Emydex and its customers and always puts service first.